|
 |
 |
制造业 中国绝对战胜不了日本之处 |
2008年12月18日 大野机械 |
既要努力开发高附加值产品,同时又要进行残酷的成本竞争。众多日本厂商在设计方面力求简单,在工厂方面努力进行生产革新,一点一滴地削减成本。其中,“
成本削减效果最大”的是零部件与材料的低价采购。再加上原油涨价的影响,今年有很多日本厂商都在为如何低价采购零部件和材料而煞费苦心。
在低价采购零部件与材料方面,如今最能够让人期待的说起来还是在中国的采购。为了顺应企业的这种需求,《日经产品制造》正在连载“中国的低价零部件选购指南”,作者曾在中国长期从事产品制造工作。令人高兴的是该连载成为深受读者欢迎的栏目之一。从这个现象也可看出,作为低价零部件与材料的供应地,很多日本厂商的技术人员都对中国寄予了巨大的期待。
而且,有的行业对中国寄予的早已超过期待。比如,在价格急剧下跌的家电、个人电脑及其外设等领域,如何从中国低价采购零部件与材料已经成为日本厂商能否生存下去的条件,这样说恐怕更接近实际情况。
中国的零部件和材料确实便宜。与在日本采购的产品相比,价格便宜3成自然不在话下。哪怕是便宜5成也极为普遍。至于电阻、加热器、连接器等通用零部件,有的甚至不足日本价格的1成。如果一家日本厂商知道这么便宜的价格以后,还不到中国去采购,一定会让人觉得不可思议。
现实情况是,众多日本厂商已经纷纷开始从中国企业采购了。即便最初会从日系的中国工厂采购零部件和材料,但后来便会逐渐地从价格更低的中国本土厂商进行采购。
但是该专栏的作者却表示,“有很多日本厂商没有搞清楚这样做风险到底有多大”。先是被价格所吸引,然后看到表面非常漂亮的工厂而大加赞叹,最后再听到品质不错的传言后,便开始彻底放心的日本企业大有人在。
确实,整体而言中国的产品制造能力已经相当高。日本一家大型工厂自动化设备企业的员工就证实说:“
直到前不久还根本不是我们对手的中国厂商,不知不觉之间对方就已经发展到了能够与本公司低价产品进行竞争的水平。
”这里之所以以工厂自动化设备为例,就是因为它是产品可靠性的一个保障。能在产品制造专业客户选择的工厂自动化设备方面得到如此之高的评价,应该说这是一个证明中国产品制造力已经得到提高的最好的例子。
但是,就目前的状况,中国在产品制造方面还存在着明显的弱点。
中国企业最大的弱点就是产品质量不稳定。尽管中国有数不清的零部件与材料厂商,但用 “ 良莠不齐 ”
来形容其质量水平是最合适不过的了。日本厂商从中国企业进行采购之初,进行严格的质量检查是必需的,但仅仅是最初则是不够的。不知道那一天就会发来一批质量有问题的零部件,而对此没有察觉的日本企业则继续使用这些零部件生产,结果在客户处出现问题的情况并不少见。
对于这种质量不稳定的现象,只要日本厂商通过严格的质量检查就应该能够解决。不过,中国制造的品质有一种是绝对赶不上日本的。这就是“特殊工序的品质”。
所谓特殊工序就是指“只要不坏,就无法判定质量好坏”的工艺(上述栏目作者)。比如,焊接工序。该栏目作者对焊接品质的低劣发出警告说,“数年前曾发生过震动整个中国市场的大事故”。欧洲一家全球著名的汽车厂商所生产的高级轿车中发现了焊接底盘脱落,这一对汽车来可谓致命的缺陷。产生缺陷的主要原因在于焊接的熟练程度太低。
像焊接这样的特殊工序单凭外观是看不出质量好坏的,因此很难采取故障保护措施。所以,在日本的汽车厂商中,一般都是由从事该工作几十年,拥有丰富知识与经验的熟练员工来承担。这也是确保日本车具有高品质的一个要素。
然而,中国的制造业虽说势头不错,但形成规模顶多也就十来年的历史。也就是说产品制造经验尚浅。因此,尤其是熟练工人人数有限,很多中国厂商都面临着熟练工人人员不足的问题。“只要到中国厂商的工厂里实际看一看,就会发现到处都是年轻员工。能指望他们确保和日本的熟练工人一样的高品质吗?尽管是特殊工序,中国企业大多也都只进行外观检查”。
与电子等行业相比,汽车行业在中国的配件采购相对滞后。其原因恐怕就是因为特殊工序在汽车配件中所占的比例较大的缘故。一位汽车行业分析师在接受采访时表示“在中国采购汽车配件不可能像预期的那样取得发展”,专栏作者也与分析师的判断异口同声,这一点令人印象深刻。这是因为汽车配件的缺陷有时候是直接关系到人的性命的,质量的波动是绝对不能允许的(注:当然并不是说其他行业就允许)。
中国制造的弱点即熟练工问题,站在日本制造的角度来看恰恰就是“宝藏”。这是因为日本企业花费大量的时间和人力培育出来的。中国的制造业无论发展的有多快,今后至少需要
10 年时间去培育熟练工人. |
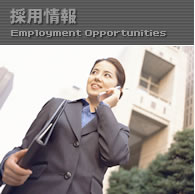 |
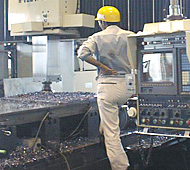 |
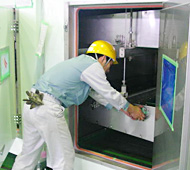 |
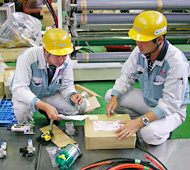 |
 |
|
|
|
|
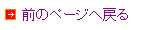 |
|
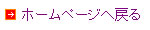 |
|
|